Blog Home > Tips and Tricks, Wood Finishing
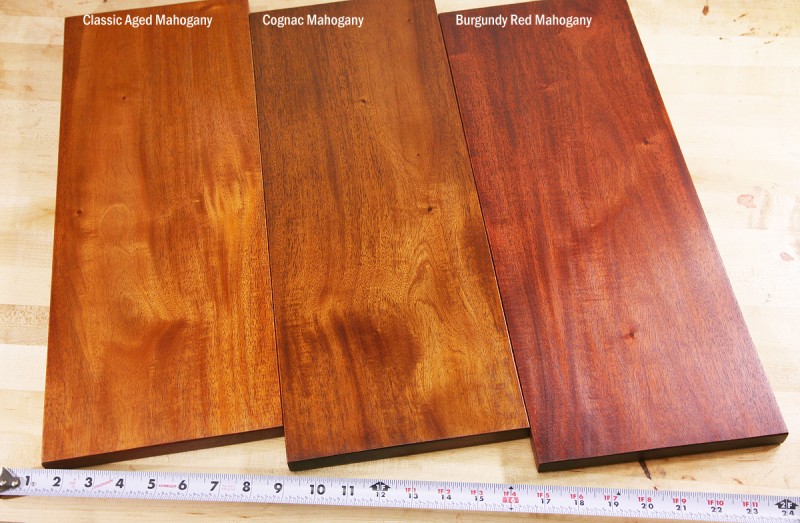
Each of these finished samples is 8″x20″ and cut from the same board – yet, you can get vastly different (and beautiful) results with a very simple technique, demonstrated below.
If you’ve seen our other tutorial on three tips for finishing mahogany, you’ll start to notice a basic four-step formula I like to employ to arrive at certain colors and characteristics:
- Dye
- Sealer
- Glaze
- Clear finish
That’s it.
Does it seem like an arsenal of chemicals? Believe it or not, the steps go quickly, and it’s actually a watered down version of what many professional furniture finishers do. So, don’t worry – this is not an uncommon practice, plus the steps you see here can be pulled off by any hobbyist woodworker with supplies found at a retail woodworking store.
There’s nothing especially proprietary with the brands and products I’ve used in the tutorial below. You can use similar colors by other brands. These just happen to be my choice because they work well and I’m accustomed to them.
I’ve performed these finishes on genuine Mahogany (Swietenia macrophylla) from Belize. But they’ll work on other types of wood such as African mahogany.
1. Classic Aged Mahogany
It’s one of the certainties when working with mahogany that once you cut it, plane it or sand it, the freshly revealed wood is disappointingly light. Mahogany needs to oxidize to its naturally coppery bronze color. Or you do this instead. Age it with a little bit of dye and a soothing, yet light, glaze of brown. The result is a wonderful and consistent warm mahogany color that very few would believe .
Products used:
- Behlen Solar-Lux NGR Dye “Golden Fruitwood”
- Zinsser SealCoat (dewaxed shellac)
- Old Masters Dark Walnut gel stain
How to do it (click an image to see captions, use ← → arrow keys to flip through each step):
Prepped by sanding to 220 grit. Does this board look unnaturally light? This is what happens to mahogany when it's freshly worked and sanded. This is normal.
mahogany-classic-finish-01
Step 1: Apply the first coat of dye
mahogany-classic-finish-02
Step 1b: After a few minutes, the dye will dry and take on a very dull (and perhaps alarmingly ugly) color tone. Do not worry.
mahogany-classic-finish-03
Step 2: Apply a thinned coat of sealer. Zinsser SealCoat is one choice because it's crystal clear, dries very fast, and has universal compatibility.
mahogany-classic-finish-04
Step 3: The sealer should dry within 10 minutes. Use a synthetic finishing pad or fine sand paper to scuff sand the surface smooth.
Step 3: The sealer should dry within 10 minutes. Use a synthetic finishing pad or fine sand paper to scuff sand the surface smooth.
Step 4: This is a technique known as glazing. Using a shop towel, apply the gel stain, then immediately wipe it off. There's a trick though. As you wipe off, first go across the grain. Don't be too firm - You should see stain streaks. Then, continue to wipe off going with the grain to eliminate the streaks. Use a gentle hand, but try to keep the coloring even. You want to leave just a haze of color on the surface.
mahogany-classic-finish-06
Step 4b: What's the purpose of the gel stain on top of a coat of sealer? This. Right side has a coat of gel stain, the left does not. The gel leaves just a kiss of color by depositing dark stain into the wood pores and a mellow coat of color to the surface.
mahogany-classic-finish-07
After the gel stain dries over night, move on to sealing once again with SealCoat, then applying your favorite clear finish.
exquisite-aged-mahogany
All finished up with a couple of coats of clear lacquer.
exquisite-aged-mahogany-3
2. Cognac Mahogany (Greene and Greene Style)
If you want less gold and more brown in your mahogany, try this. It’s a variation on the Greene and Greene style recipe by Darrel Peart that begins by mixing 7 parts orange to 4 parts medium brown dye, then diluting the mixture and applying it in a series of coats. (Applying dye in several diluted coats is a good practice). Instead, this mix is 5 parts orange to 4 parts brown. The only difference between this finish and the “Classic Aged Mahogany” above is the addition of the brown dye.
Products used:
- Behlen Solar-Lux NGR Dye “Golden Fruitwood”
- Behlen Solar-Lux NGR Dye “Brown Maple”
- Zinsser SealCoat (dewaxed shellac)
- Old Masters Dark Walnut gel stain
How to do it (click an image to see captions, use ← → arrow keys to flip through each step):
Start by mixing a batch of dye in a mixing cup. Try a 5:4 ratio of Golden Fruitwood to Brown Maple. Then move on to these steps, which are essentially the same as above.
Here's our work piece for this recipe. The board of mahogany is prepared by sanding through the grits to 220.
mahogany-cognac-brown-01
Step 1: Apply the dye. Once it dries, slightly sand it if the grain has raised, and decide if it needs another coat or not.
mahogany-cognac-brown-02
Step 2: Apply a coat of sealer (Zinsser SealCoat used here). Thin it with denatured alcohol for better control.
mahogany-cognac-brown-04
Step 3: Scuff sand the sealer as needed. The surface should be smooth and flat.
mahogany-cognac-brown-05
Step 2b: After the sealer dries, inspect your surface and be sure it's smooth and flat.
mahogany-cognac-brown-06
Step 4: Use the gel stain to glaze the wood. Apply it in a circular motion.
mahogany-cognac-brown-07
Step 4b: Once the work area is covered, wipe it off with a clean cloth or paper towel. Gently wipe across the grain, then wipe with the grain to blend in any streaks. Do not wipe too aggressively, it's important to have a mild coat of color left on the surface
mahogany-cognac-brown-08
Here's the result immediately after the gel stain. The glaze has a modest, pleasing effect. Allow it to dry over night, then apply your favorite clear finish on top.
exquisite-cognac-mahogany
All finished with two coats of clear lacquer
exquisite-cognac-mahogany-3
3. Burgundy Red Mahogany
Going further, you can take that same mix of dye that’s used in the cognac color above and just add a little bit of reddish purple to arrive at a starkly different color.
Products used:
- Behlen Solar-Lux NGR Dye “Golden Fruitwood”
- Behlen Solar-Lux NGR Dye “Brown Maple”
- Belen Solar-Lux NGR Dye “Medium Red Mahogany”
- Zinsser SealCoat (dewaxed shellac)
- Old Masters Dark Walnut gel stain
How to do it (click an image to see captions, use ← → arrow keys to flip through each step):
Start by mixing a batch of dye in a mixing cup. Use 5:4:2 ratio of the dyes in this order Golden Fruitwood:Brown Maple:Medium Red Mahogany Then do the same application process.
Here's the board sanded and prepped for finishing. Like the others, the color starts quite pale, but this is normal with freshly worked mahogany.
mahogany-old-red-finish-01
Step 1: Apply the dye solution.
mahogany-old-red-finish-02
After two coats of dye, the color on this came out too dark for my taste. Fortunately, it's stress-free fix.
mahogany-old-red-finish-03
Step 2: If you find the dye is too dark, give it a wipe down with denatured alcohol and a clean rag. If that lifts enough color, then move on to the next step. Otherwise, you can lighten the dye by scuff sanding with a 220-grit sponge.
mahogany-old-red-finish-05
Step 3: Seal the dye with a thin coat of Zinsser SealCoat or another compatible sealer. After it dries, check it for areas that need to be sanded smooth and sand carefully.
mahogany-old-red-finish-04
Step 4: Wipe on a coat of dark brown gel stain, then immediately wipe it off.
mahogany-old-red-finish-07
Step 4b: to wipe off, work across the grain gently with a clean rag or shop towel. Then go with the grain to blend in the streaks. Work gently enough not to remove too much gel stain.
mahogany-old-red-finish-08
Immediately after the gel stain, here's the effect. Let it dry over night, then proceed with a clear top finish.
exquisite-burgundy-mahogany
All finished with two coats of clear lacquer
exquisite-burg-mahogany-3
Vice President of Operations – Woodworkers Source
We’re a family-owned lumber & woodworking supply retailer with 3 delightful stores in Arizona, and 35 friendly employees.
Mark oversees the company and creates tutorials on wood finishing and woodworking tips for hardwood lumber.
Woodworkers Source is a division of MacBeath Hardwood Co.
Discussion, Questions & Answers