Blog Home > Tips and Tricks, Woodworking Projects
In this guest blog post, Jim King takes on a tour, so to speak, of his turning shop down in Peruvian Amazon. I hope you enjoy his humor and enlightening pictures from a fairly primitive set up.
– Mark Stephens
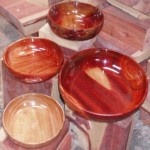
Typical of the woods and turnings
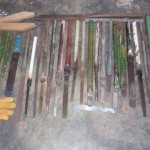
My tools are made of car springs, old files, wrench handles, a broken off machete ....
Wood turning is one of the oldest crafts in the world and has been done with very primitive but creative tools. Most of the world does not have the big boys’ toy stores for woodworkers as in North America, but woodworking still goes on all over the world.
A typical Amazonian turning shop is a little rough around the edges. The electricity comes and goes and materials and tools may or may not be found. One thing is very noticeable, and that’s no one complains.
I will show how wood turning gets done with tools that would be banned in many parts of the world. The carpenter shop shown and described here was mine in the Upper Amazon of Peru. Coming from a woodworking background where I had a sander for each problem and tools of any and all types I had to reinvent myself in the Amazon. When you are in desperate need of a tool or machine to do a job and have a good bottle of rum to make the mind move, solutions just appear.
Here is a photo of my lathe and some of the tools. The lathe was made of some pipe and iron from an oil company and cost almost $300 complete. It works well but the head stock and tail stock are about ¼ inch from being aligned. Amazing but that creates very little problem. I don’t know how many RPMs it turns; the plate on the motor was missing as it was probably stolen somewhere along the line. I would guess it to be about a five horse and it does go fast.
Enjoy the pictures and commentary.
HAPPY TURNING FROM THE JUNGLE
-
-
-
The tools are made of car springs, old files , wrench handles , a broken off machete for a parting tool, once in a while some good steel and the handles are iron pipe. I like heavy tools. The store bought tools make me feel like I am working with a finger nail file . I don’t feel safe with them.
-
-
Screw plates made with a bolt and some steel plate
-
-
The $18 dollar Chinese sharpening system
-
-
Here we are at the local flea market picking out the new iron to be made into our tools
-
-
A local shop cutting car springs to half the width. Most of the tools are Toyota brand.
-
-
Cutting the blank as round as possible (with precision and utmost safety . . .)
-
-
Rounded blanks ready for turning
-
-
Rough turning the form
-
-
rough turned pieces ready for boiling (This boiling process virtually eliminated the cracking and warping.)
-
-
Boiling the rough turned pieces prior to drying.
-
-
A dryer with a couple of light bulbs and fans
-
-
Pieces after being boiled left to air dry for a couple of months before drying in the dryer
-
-
Returning the dried rough out
-
-
Sealing the turning for sanding and ready for final coats of floor grade polyurethane
-
-
Wet sanding with soap and water and buffing with car buffing compound
-
-
The donut chuck made from ¾ ply and shoe sole material for finishing off the bottoms
-
-
Beautiful stuff
-
-
Looks nice, doesn’t it?
-
-
Every year we put a show in the Dept of Natural Resources booth to display unused species.
-
-
Typical of the woods and turnings
-
-
Typical of the woods and turnings
-
-
Typical of the woods and turnings
-
-
Step 1: This is the first step of an inside out. Here are 4 pieces of 4 x 4 x 39 held together by plywood face plates screwed onto each end. This will be the inside when done
-
-
Step 2: This photo shows the 4 pieces taken apart and turned inside out. Now for turning the outside after the glue dries.
-
-
Step 3: when turning the outside it sounds like a helicopter in the room and you wonder if you should really be doing this. The hose clamps are to make a person feel better, I don`t think they did much.
-
-
This is the finished piece. A nice little beer cooler.
-
-
I was a little bit worried about my helper. With the big, long sturdy tools I was worried that if he got a catch he would have a problem. The solution was to make him a super turner outfit so when he got the catch and launched he didn´t get hurt. The shop was accident free and the safety equipment was minimal. I had a hard time keeping shoes on the people much less other things.
-
-
This was Rickey the guard dog. He didn`t have many teeth left when he showed up but he looked tough.
-
-
Vice President of Operations – Woodworkers Source
We’re a family-owned lumber & woodworking supply retailer with 3 delightful stores in Arizona, and 35 friendly employees.
Mark oversees the company and creates tutorials on wood finishing and woodworking tips for hardwood lumber.
Woodworkers Source is a division of MacBeath Hardwood Co.
Discussion, Questions & Answers